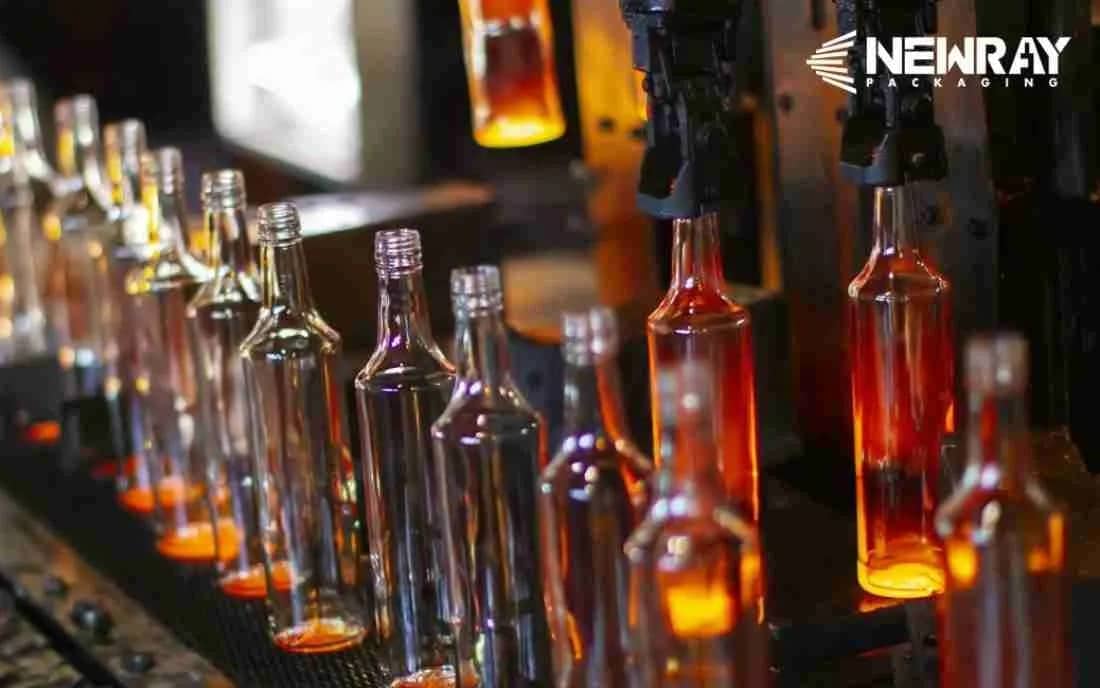
Nowadays, glass packaging containers are a kind of product that we often see in our daily lives. Compared to other plastic products, paper products, iron products, etc., glass containers have some advantages that products made of other materials cannot match.
Advantages of glass packaging materials:
1. The glass material has good barrier properties, which can prevent oxygen and other gases from invading the contents, and can also prevent the volatile components of the contents from evaporating into the atmosphere;
2. Glass raw materials can easily change color and transparency with no any harm;
3. Glass bottles and jars can be used repeatedly, which can reduce packaging costs;
4. Glass bottles are hygienic, have good corrosion and acid corrosion resistance, and are suitable for packaging acidic substances (such as fruit and vegetable juice drinks, etc.);
5. In addition, because glass bottles are suitable for the production of automatic filling production lines, the development of automatic filling technology and equipment for glass bottles at home and abroad is also relatively mature. Using glass bottles to package fruit and vegetable juices and beverages has more production and competitive advantages in the market.
However, during the production process, some of the glass factory that produced bottles may have poor smoothness, so today Newray will analyze from a professional perspective what factors will affect the smoothness of glass bottles?
1. When the glass blank falls into the preliminary mold, it cannot accurately enter the preliminary mold, and the friction with the mold wall is too large, forming wrinkles. After positive blowing, the wrinkles spread and enlarge, forming wrinkles on the glass bottle body.
2. The scissor marks of the upper feeder are too large, and the scissor marks appear on the glass bottle body after individual bottles are formed.
2. The initial mold and final mold of the glass wine bottle are made of poor materials and have insufficient density. They oxidize too quickly after high temperatures, forming tiny pits on the surface of the mold, causing the surface of the molded glass packaging bottle to be dull.
4. Poor quality of glass bottle mold oil will cause insufficient lubrication of the mold, slow down the dropping speed, and change the material type too quickly.
5. The design of the preliminary mold is unreasonable, and the mold cavity is large or small. After the material drops into the mold, they are blown and spread unevenly, which will cause spots on the glass bottle body.
6. The machine’s uneven dripping speed and improper adjustment of the air nozzle will cause the temperature of the initial mold and the finished mold of the glass bottle to be inconsistent, which will easily create cold spots on the body of the glass wine bottle, directly affecting the smoothness.
7. If the glass liquid in the kiln is not clean or the temperature of the material is uneven, bubbles, small particles, and small hemp blanks will appear in the produced glass bottles.
8. If the machine speed is too fast or too slow, the glass bottle body will be uneven, the bottle wall will be of different thicknesses, and spots will occur.
The appearance quality problems of glass bottles are related to whether the production equipment is high-precision equipment and the expertise of skilled workers. In order to prevent bottle wrinkles, Newray glass manufacturer imports advanced equipment and technology from Germany and continuously increases investment in basic equipment and technical personnel. It can continue to innovate while maintaining high quality and be at the forefront of the same industry in the world.
Because some small factories do not have formal production processes and have no professional technical workers, or the workers are not rigorous in their work and do not replace the appropriate scissors according to the size of the glass material type, this will lead to defects in the glass bottles produced and sold to the outside world.
The Newray glass bottle factory has strict quality control over every detail of the products it produces. All products produced require quality inspection at all levels. The fully automatic inspection equipment can automatically remove unqualified products, including water marks, bubbles, stones, and cracks. etc. defects.
Quality inspectors will randomly inspect at least 3 products per mold number every hour to check whether each parameter meets the standards and whether the appearance is qualified. The staff of the physical and chemical performance laboratory will also inspect each production batch of products, check the products against the corresponding testing standards according to the product use, and issue a product inspection report. Let all customers receive 100% satisfactory glass bottles that meet international acceptance standards.
The mold factories that Newray Packaging Solutions cooperates with are among the five most famous mold factories in China. The materials and production processes of the molds are first-class at home and abroad, and the after-sales services are guaranteed. In the production of glass packaging containers, molds are a very important step. Newray adheres to the purpose of providing customers with the best products and does not save costs on molds. Carry out professional design and review and review by technical managers at all levels. Supervise the quality control of mold blanks in the mold factory and ensure the quenching time of mold production. We do not save some important production process in order to meet the deadline. If a worker wants to do his job well, he must first sharpen his tools. Newray always treats the mold design and product production of each batch of orders with a rigorous attitude.
Our Newray Glass bottle factory has our own chemical new energy laboratory and we are in-depth cooperation with authoritative third-party testing institutions. We have strict control over upstream raw materials. Each batch of raw materials is tested accordingly every day and must meet the factory standards before all the glass raw materials can be produced and used. This ensures that the physical and chemical properties and new chemical properties of the glass bottles produced can always be within the control range and meet the different standard requirements of different customers.
Newray, provides customers with assured products and is committed to customer success!